history of printing
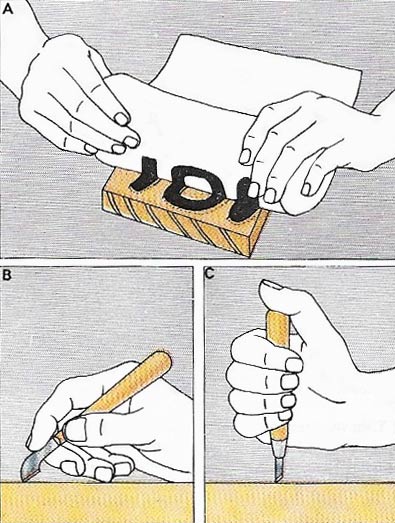
Figure 1. The woodcut was developed from the 15th century onwards to produce devotional prints and playing cards. The artist cuts away the part of the design that is to appear white, so that only the parts to be inked appear in relief (A). The block is cut along the grain using well-seasoned wood from apple, pear, cherry, sycamore, or oak trees. Some early woodcuts were hand-colored but prints can be produced by using a series of blocks. A variety of tools were used, such as the English knife (B) and the Japanese knife (C).
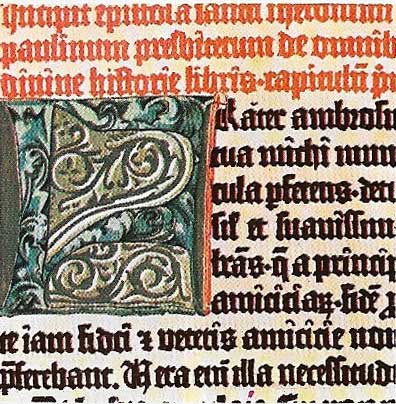
Figure 2. The first substantial book printed from movable type was the Latin Bible published in Mainz, Germany, in 1456. This remarkable book has 643 leaves, each page printed in two columns of 42 lines. Known after its celebrated printer, Johannes Gutenberg, as the Gutenberg Bible, it is not only the first major product of modern typography, but is still among the finest examples of the printer's art. This illustration, taken from a page of the Bible, shows the typeface used by Gutenberg. This face was known as Textura and it was cut to resemble the manuscript hand used in the 15th century in Germany to prepare handwritten Bibles and church service books. The Gutenberg Bible was printed in 10 sections on six presses at once, the edition running to 150 copies on heavy paper and 30 on fine vellum.
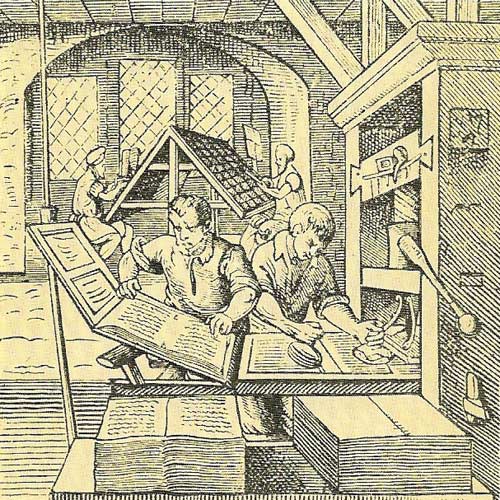
Figure 3. Printing from movable type radically improved the dissemination of knowledge about scientific discoveries in Europe by the 16th century. This woodcut of 1568 by Jost Amman shows a printing works with composers setting up type in the background, while in the foreground the press is being operated.
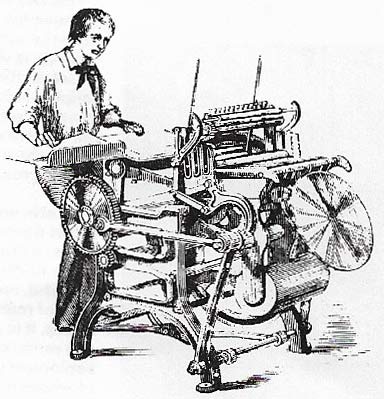
Figure 4. The first self-inking treadle platen press was designed and built by an American, Stephen Ruggles, in 1839. This improved design built by him 12 years later became the model for the popular jobbing press. In this machine the forme of type is clamped in a near-vertical position. Above the form is a rotating disk that serves to distribute the ink. Three composition rollers roll down over the disk, picking up ink and then down over the type forme. When the rollers have returned, the platen (on which the paper has been laid by hand) moves up against the type form.
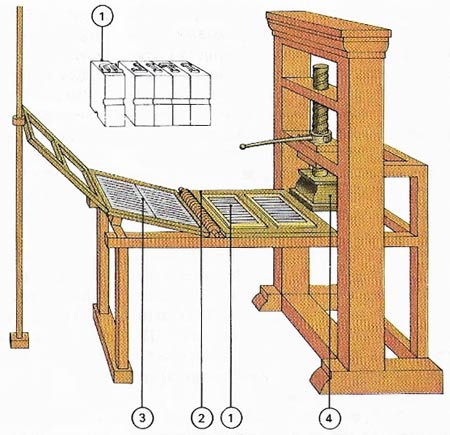
Figure 5. Early printing presses resembled 15th-century linen presses. The type matter (1) was wedged in a sliding tray (2) and then inked by hand. The paper was placed on a parchment covered 'tympan' (3) which hinged into position over the type tray. This slid under the screw-down press (4).
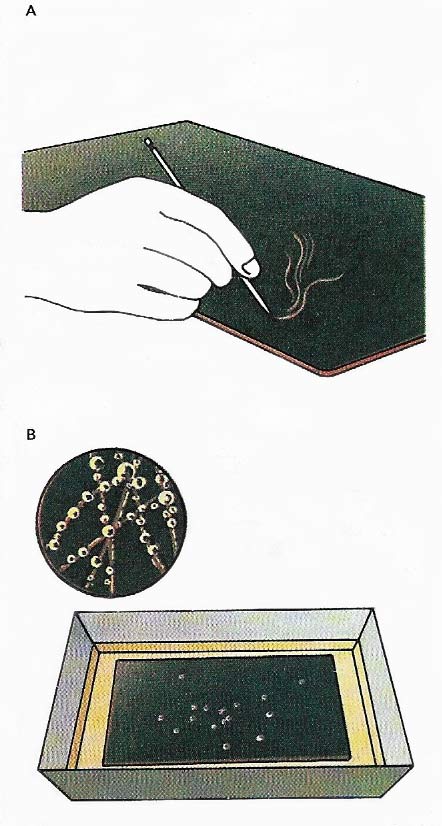
Figure 6. In an etched printing plate the ink fills the grooves made by acid in a polished metal plate (copper, zinc, aluminum, or steel). The plate is coated with acid-resisting wax. The image is drawn in the wax with an etching needle (A) exposing the metal. The scribed plate is then put in acid (B) which eats into the metal where the wax has been removed. After cleaning off the wax the plate is inked, then wiped.
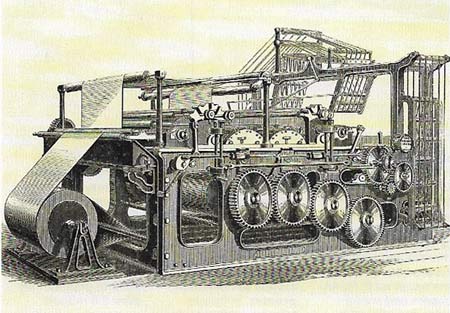
Figure 7. The principle of printing on paper fed from a roll with the sheets being cut after printing was invented Rowland Hill (1795–1879), who later introduced the penny post in England. Rotary machines were developed for newspaper printing from 1846, using curved stereotypes cast from curved paper mache molds (flongs) of the original flat type formes. This early Victory press printed at speed from a paper roll (web) and folded the cut sheets.
Movable metal type was probably first produced in the Royal Type Foundry of Korea in 1403 and a book was printed from this type six years later. But not until 1439 is there evidence of printing, as we know it today, in Europe. It was a German, Johannes Gutenberg (1400–1468), working in Strasbourg, who developed printing using movable type.
Early printing methods
In the year 1456 the first substantial printed book appeared. This was a Latin Bible printed in Mainz, almost certainly by Johannes Gutenberg and his associates (Figure 2). How Gutenberg manufactured his type is not known and it was not until 1540, in Vanoccio Biringuccio's book De la pirotechnia, printed in Venice, that there was a description of type-founding. Type was made by pouring molten metal into a copper matrix or mould formed by punching an engraved steel character into a piece of copper.
From the days of Gutenberg there were, for many centuries, no significant changes in the basic methods used for printing. Metal type was set by hand pages known as formes and these were inked and printed on to single sheets of paper in a hand press. The first change came in 1795 when Firmin Didot (1764–1836) tested ways of making duplicate printing plates (stereotypes) from type set.
Three years later lithography was invented by Aloys Senefelder (1771–1834) of Munich. While seeking a practical method of printing musical scores he tried drawing the music in reverse on a flat slab of stone, using an ink made of wax, soap and lamp-black. His original idea was to etch the stone with acid but his experiments led to an entirely new printing process based on the mutual repulsion of oil-based ink and water.
![]() |
Lithography is based on the mutual repulsion of greasy ink and water. The image to be printed is drawn, in reverse, on stone using a greasy pencil or ink. The stone is then soaked in water and inked. The ink adheres to the image but not to the wet stone. The machine (above) presses paper from the holder on to the stone, thus making the print. The process was used originally for printing hand-drawn music (below).
|
![]() |
From plates to printing machines
Didot's stereotype process was perfected in 1800 by Charles Stanhope, third Earl Stanhope (1753–1816), who used plaster of Paris to make the moulds of the type set. Molten metal was then poured into the plaster moulds to produce solid printing plates, a whole page at a time. In 1806 Anthony Berte of London invented a mechanical device for typecasting, using a pump to force molten metal into the matrix.
In the meantime Fredrich Konig (1774–1833), a German printer who moved to England in 1806, built the first successful printing machine in which a series of leather-covered rollers, fed with ink from a container, automatically inked the type as it travelled to and from the printing platen. Except for the laying on and removing of the paper from the platen, this steam-powered press was automatic. In the following year Konig designed a cylinder printing machine in which the type forme was fixed to a bed which moved first under the leather-covered inking rollers and then under a cylinder around which the paper was held. Soon after the first single-cylinder machine was successfully demonstrated in London two machines, each with twin cylinders, were manufactured.
Nineteenth-century progress
In 1816 an Englishman, Edward Cowper (1790–1852), secured a patent for a method of bending stereotype plates for rotary printing, the plate first being cast flat in a plaster mould of a type forme. In the same year Friedrich Konig and Andreas Bauer (1783–1860) built the first perfecting machine – which could print on both sides of the paper.
A traditional printing press uses mirror image type. In 1817 and Englishman, called Augustus Applegath (1788–1871), designed a machine to print bank-notes with the same design on each side of the paper and with each color in perfect register with the others. In this machine a curved stereotype first printed on to a leather pad fitted around the printing cylinder. When one revolution was complete the paper was fed between the stereo and the leather pad so that the metal printed on one side of the paper and the inked leather pad on the other. The idea was to produce bank-notes that could be forged only with difficulty, and Applegath's machine in fact printed the lower side of the notes by what is now called the offset method. The leather pad was printed with a mirror image of the original type matter which it then transferred to the paper. As a result the printed image on the lower side of the paper was identical to the original stereo. This principle was later made use of in offset printing, in which the type matter is identical to the finished print.
The next 70 years saw numerous advances in the art of printing. Stereotype preparation from papier mache moulds was originated by Claud Genoux of Lyons. These moulds or "flongs" were strengthened with clay and glue. In 1845 the French printing firm of Worms and Phillipe patented the idea of casting curved stereos direct from a curved flong. This is the method still used in most newspaper printing today.
In 1838 the American David Bruce, Jr (1802–1892) built the first commercially successful mechanical typecasting machine, which made 100 characters in an hour. In 1852 the first printing by photolithography was carried out experimentally by Alfred Lemercier, a Frenchman. Lemercier coated his printing stone with a light-sensitive substance which was exposed through a paper negative. After washing with turpentine the design on the stone could then be inked for normal lithographic printing.
![]() |
The linotype composing machine, invented by Pttmar Mergenthaler (1854–1899), an American of German parentage, was probably the greatest single printing innovation of all time. The machine was first used to typeset the New York Tribune in 1886. The operator 'types' the copy on a keyboard and the machine sets letter molds (matrices) in the correct order. At the end of each line a complete line of type (slug) is cast in one piece.
|