Delta
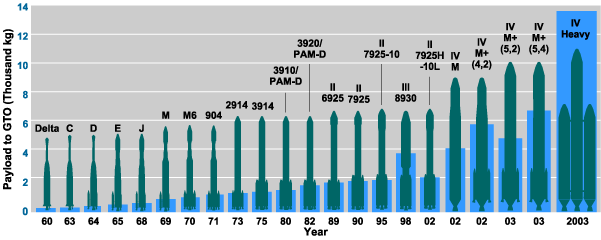
Evolution of the Delta. Courtesy Boeing.
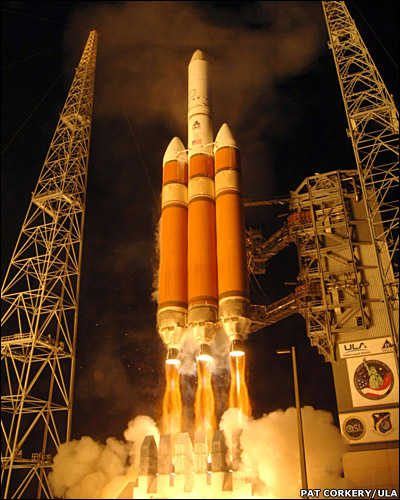
Launch of Delta IV Heavy carrying a classified military payload.
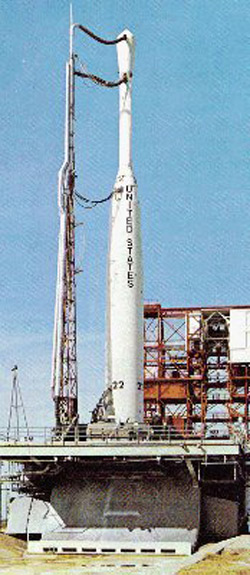
Delta B carrying Tiros 8.
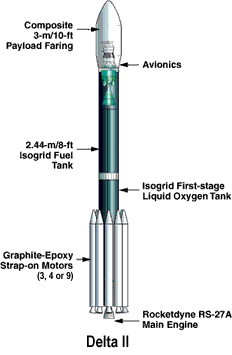
Delta II.
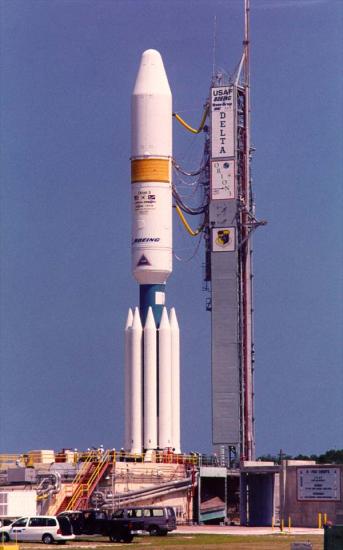
Delta 3. Courtesy Boeing.
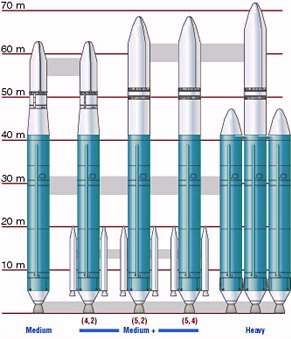
Delta 4 family. Courtesy Boeing.
The Delta family of launch vehicles was derived from the Thor ballistic missile for the purpose of placing intermediate-mass civilian payloads into orbit. First introduced in 1960 and manufactured by Douglas Aircraft, the Delta was conceived as a short-term solution to NASA's launch needs of that era, but continued to evolve and remains in use today in various versions of the Delta II and Delta IV.
The Thor had already been adapted for satellite launches using a variety of upper stages, giving rise to the Thor-Able, Thor-Able Star, and Thor-Agena A. The intended name Thor-Delta reflected the fact that this was the fourth upper stage configuration of the Thor-based space launch vehicle. However, since the vehicle was designed mainly as a civilian satellite launcher, the military name Thor was dropped. The same naming principle was applied in the late 1950s as the Redstone-based and Jupiter-based rockets were renamed Juno I and Juno II, respectively, for civilian satellite launching. But as far as extant missile-descended rocket families are concerned, the Delta is unique: the Atlas and Titan retained the names of their military ancestors.
History
The original Delta was a three-stage launch vehicle consisting of a Thor first stage mated to improved Vanguard upper stages. The first Delta, launched on 13 May 1960, and carrying Echo 1, failed due to a second-stage attitude-control problem. However, the Echo 1 reflight, three months later, was a total success. In 1962 Douglas Aircraft began a series of upgrades and modifications that would increase the Delta's capacity tenfold over the next nine years.
The Delta A was almost identical to the original Delta but had an upgraded Rocketdyne first stage engine. The Delta B, with an improved guidance and electronics system and longer second-stage propellant tanks (to increase fuel capacity) and an upgraded Aerojet second-stage engine, launched the world's first geosynchronous satellite, Syncom 2. The Delta C was similar to the B but with a bulbous fairing to make room for bigger payloads and a new, more powerful third stage solid-rocket motor, developed for the Scout rocket.
With the Delta D, originally known as the Thrust Augmented Delta (TAD), was introduced a major improvement that became a Delta trademark. Three Castor 1 solid rocket boosters (SRBs) were added to augment the thrust of the first stage engine (which was itself upgraded) and thus the overall payload capacity. This strap-on configuration had already been applied successfully to the Thrust Augmented Thor-Agena D. Ignited at liftoff and jettisoned during flight, the SRBs gave the Delta the extra thrust needed to place operational Syncom satellites into GTO (geostationary transfer orbit).
The Delta E, originally called the Thrust Augmented Improved Delta (TAID), came with a further upgraded first stage engine and more powerful Castor 2 SRBs. The second stage was made restartable and its propellant tanks widened. The third stage motor was either that from the Delta D or a more powerful Air Force-developed motor, and the payload space was made still larger using an Agena fairing. A two-stage version of the E, known as the Delta G, equipped with a reentry vehicle, was specially made to carry Biosatellite-1 and -2 into LEO. Delta J featured a new third stage Star motor.
Referred to as a Long Tank Delta (LTD) or Long Tank Thrust Augmented Delta (LTTAD), the Delta L used the new Long Tank Thor first stage with its lengthened propellant tanks. The L, M, and N models were identical except for their third stage configurations. The Delta L used the same third stage motor as the E. The Delta M used the same third stage as the J, while the M-6 variant was the same as the M but with the addition of three more Castor 2s, for a total of six. The Delta N was a two-stage version of either the L or M, and the N-6 a two-stage version of the M-6.
With the 900 series came an important evolutionary step in the Delta program, and a vital link to the Deltas that followed. The Delta 900, which came in two-stage (900) and three-stage (904) versions, featured nine strap-on Castor 2s and an improved guidance and electronics package. The second stage used a more powerful Aerojet engine, the AJ-10, previously flown as the Titan Transtage.
All subsequent Deltas used a four-digit numbering system for model identification. The first digit indicates the first stage and SRB type. For example, all 6000-series models employ the Extra Long Extended Tank Thor first stage with a Rocketdyne RS-27A main engine and Thiokol Castor 4A SRBs. The second digit tells how many SRBs are used – 3, 4, 6, or 9. The third digit indicates the type of second stage-0 (Aerojet AJ10-118F), 1 (TRW TR-201), 2 (Aerojet AJ10-118K), or 3 (Pratt & Whitney RL10B-2). The fourth digit tells the third stage type-0 (no third stage), 2 (FW-4), 3 (Star 37D), 4 (Star 37E), 5 (Star 48B PAM-D derivative), or 6 (Star 37FM).
Introduced in the early 1970s, the 1000 series was the first Delta to be based on the Extended Long Tank Thor configuration that came to be known as the "straight-eight." While previous Deltas were tapered at the top, the Delta 1000 kept the 2.4-meter first-stage diameter over its whole length, except for the rounded conical tip of the payload fairing. Since the upper stage diameters were now the same as the first stage, extra room was available at the top of the rocket for larger payloads. Otherwise identical to the Delta 900, the 1000 came in eight two- and three-stage variants. The five models of the 2000 series, flown mainly in 1974–1979, incorporated more improvements. Although the same SRBs were used as in the Delta 900 and 1000, the first and second stages were completely upgraded. The first stage engine was adapted from the H-1 Saturn I and IB first stages, and the second stage engine from the Apollo Lunar Module main engine. Configuration options included two or three stages, and three, four, six, or nine SRBs.
Born of the need for a rocket capable of carrying payloads too heavy for the Delta 2000 but not heavy enough to require use of an Atlas-Centaur, the 3000 series was introduced in the late 1970s and early '80s. Since NASA did not envision a need for a new medium-weight launch vehicle so close to the introduction of the Space Shuttle, the Agency was reluctant to finance this next generation Delta. However, it did see a use for the 3000 as an interim vehicle to handle medium-weight payloads prior to operational flights of the Shuttle. As a result, McDonnell Douglas was able to secure private industrial financing to develop the 3000. NASA financed no R&D, but bought the completed vehicles to support civilian and commercial satellite launches. Although similar in design to the Delta 2000, the 3000 used powerful new Castor 4 SRBs. A Payload Assist Module (PAM) was offered as an optional third stage, enabling larger payloads to be carried to GTO. An improved PAM, called PAM-D, was later introduced which further increased the 3000's capacity.
The 4000 was to have been Delta's swansong at a time when virtually all commercial, civilian, and military satellite delivery duties were being switched to the Shuttle. But in the early 1980s McDonnell Douglas proposed improvements to further boost the Delta's GTO capacity. Although the Delta program was waning at the time, this goal was met by increasing the first stage burn time and bringing in other technical innovations. Nine Castor 4s were used as in the Delta 3000, but in the 4000 configuration six of them were typically ignited at launch, with the remaining three ignited following burnout and jettison of the first six. The first stage fuel tanks were lengthened to give a longer first-stage burn time and improved performance. In the first departure from the straight-eight configuration, the 4000 introduced a payload fairing adapted from the Titan IIIC program to make room for larger payloads. The greater size of the 4000 demanded costly modifications to support structures at Cape Canaveral and Vandenberg Air Force Base. While these expenses may have seemed risky, McDonnell Douglas' investment in the 4000 proved fruitful. Although Delta production officially ceased in 1984 following 24 years of service as a workhorse of the civilian, commercial, and military satellite launch industry, the Delta retirement was short-lived.
Delta II
Like the Atlas family of space launchers, the Delta program faced cancellation in the early 1980s as the Shuttle took on more satellite launching duties. However, the Challenger disaster graphically showed that the American civilian, commercial, and military satellite industries still needed reliable expendable launchers. With priorities for the Shuttle fleet dramatically shifted, an improved Delta filled a gap, as had previous Deltas, in providing a rocket capable of launching a wide spectrum of medium-mass payloads. An immediate need for post-Challenger expendable vehicles was created when NASA announced that commercial satellites would no longer be carried aboard the Shuttle. However, it was the military that facilitated the official rebirth of the Delta program. The Air Force signed a renewable contract for 20 Deltas to begin launching GPS satellites in 1989. A new and improved generation of Delta launch vehicles was introduced under the name Delta II.
Based largely on the Delta 4000 already in use, the 6000 boosted performance by incorporating nine improved Castor SRBs. Six of these were ignited at liftoff, with the remaining three ignited following burnout and jettison of the first six. The basic nine-booster Delta flight profile has not changed since.
The current version of Delta II, the Delta 7000, comes in a variety of two- and three-stage forms, and uses new strap-on SRBs known as graphite epoxy motors (GEMs) for improved performance.
The Delta II bears little resemblance to the original Thor-Delta. With a height of 41 meters, the Delta 7925 stands over 10 meters taller than its ancestor and has a GTO payload capacity of about 1,870 kilograms – more than 40 times that of the Thor-Delta. Depending on mission needs. Delta II payload delivery options range from about 891 to 2,142 kilograms (1,965 to 4,723 pounds) to geosynchronous transfer orbit (GTO) and 2.7 to 6.0 tonnes (5,934 to 13,281 pounds) to low-Earth orbit (LEO). Two-stage Delta II rockets typically fly LEO missions, while three-stage Delta II vehicles generally deliver payloads to GTO or are used for deep-space explorations such as NASA's missions to Mars, a comet, or near-Earth asteroids.
The first stage is powered by the Boeing Rocketdyne-built RS-27A main engine and by Alliant Techsystems' solid rocket strap-on GEMs for added boost during liftoff. Boeing configures Delta II with three, four or nine GEMs for various performance capabilities. When nine GEMs are used, six are ignited at liftoff and three are lit once the rocket is airborne. When three or four GEMs are used they are all ignited at liftoff.
Aerojet's AJ10-118K engine powers the storable propellant restartable second stage. The Thiokol Star-48B solid rocket motor propels the optional Delta II third stage.
The Redundant Inertial Flight Control Assembly (RIFCA), built by L3 Communications Space & Navigation (formerly AlliedSignal Aerospace), is another key second-stage component. It provides guidance and control for the rocket resulting in the precise payload deployment that is associated with Delta II launch services.
Delta II can launch single, dual, or multiple payloads on the same mission. To accommodate these varying requirements, Boeing designed a variety of payload attach fittings. The company also builds several fairing types to enclose and protect payloads on the launch pad and during ascent. A composite fairing is offered in a 3 meters (10 feet) diameter size. An aluminum 2.9 meters (9.5 feet) diameter fairing is available, as is a 3 meters diameter stretch composite fairing for certain payloads.
Delta III
Almost four decades of continual development increased the Delta's payload capacity by steady increments. The Delta III, however, represented a sudden leap in capacity to over twice that of the largest Delta II. A major part of this improvement was due to the Delta III's second stage, powered by a Pratt & Whitney RL10B engine derived from the RL10 that has been the basis of the Centaur for over 30 years. Burning liquid hydrogen and liquid oxygen, the RL10B has a world-record specific impulse rating (an efficiency measure) of 462 seconds and represents the first use of a high-energy cryogenic engine in a Delta. Additionally, new SRBs supply 25% more thrust, and three of the boosters are equipped with thrust vector control for better maneuverability. A new 4-meter-diameter payload fairing tops the assembly. The first Delta III was launched in August 1998 and, like the very first Delta, carried a real payload – the Hughes Galaxy-X communications satellite – rather than a test article. Unfortunately, it also suffered the same fate, as a directional control problem doomed the flight. The second Delta III launch, in May 1999, also failed due to a rupture in the thrust chamber of the RL10 engine. The third flight, on 23 August 2000, was successful but ironically carried only a test payload.
Although the Delta III had a backlog of launches, its manufacturer, Boeing, phased it out in favor of the Delta IV.
Delta IV
The latest extension of the Delta dynasty; it was developed under the Air Force EELV contract. The Delta IV is composed of five vehicle configurations based on a new, liquid oxygen/liquid hydrogen common core booster powered by single RS-68 engine. Delta IV second stages are derived from the Delta III second stage, using the same RL10B-2 engine, but with two sizes of expanded fuel and oxidizer tanks, depending on the model. Together, the Delta IV variants are capable of replacing not only the current Delta IIs and IIIs but also the more powerful Titan IV.
The first Delta IV launch took place on 20 November 2002, and successfully placed the Eutelsat W5 satellite in orbit. Subsequent Delta IV launches took place on 10 March 2003 (DSCS III A3), 29 August 2003 (DSCS III B6), and 21 December 2004 (Delta IV Heavy demonstration flight). The inaugural Delta IV Heavy rocket suffered premature engine shutdowns during its December test launch because of bubbles in the liquid oxygen plumbing, a problem that will hopefully be rectified by the time of the first operational launch of the vehicle in October 2005. The three engines closed down several seconds early after internal sensors mistakenly identified the liquid oxygen fuel supply as having been expended. This left the rocket with a massive underspeed, which the vehicle's upper stage could not overcome, and resulted in a final orbit lower than planned. The Delta IV Heavy is the largest member in Boeing's next-generation rocket family. It takes three Common Booster Cores, each featuring a cryogenic main engine, and straps them together to form a vehicle capable of launching hefty cargos into space.
version | length (m) | diameter (m) | stages | thrust (N) | payload/LEO | GTO | GSO | escape |
Original Delta | 27.4 | 2.4 | 3 | 270 | ||||
1st stage (LOX/RP-1) | 670,000 | |||||||
2nd stage (IRFNA/UDMH) | 34,000 | |||||||
3rd stage (solid) | 12,400 | |||||||
Delta A | 3 | 320 | ||||||
1st stage | 760,000 | |||||||
Delta B | 28.3 | 2.4 | 3 | 375 | 68 | |||
Delta C | 3 | 410 | 80 | |||||
Delta D | 3 | 580 | 105 | |||||
1st stage | 775,000 | |||||||
+ 3 strap-ons | 696,000 | |||||||
Delta E | 29.2 | 3 | 725 | 150 | ||||
2nd stage | 34,000 | |||||||
3rd stage | 26,000 | |||||||
Delta G | 29.5 | 2 | ||||||
Delta L | 32.4 | 3 | ||||||
Delta M | 32.4 | 3 | 1,000 | 355 | ||||
Delta M-6 | 1,300 | 450 | ||||||
Delta N | 2 | |||||||
Delta 900 | 32.4 | |||||||
902 | 2 | 1,680 | ||||||
904< | 3 | 640 | ||||||
Delta 1000 | 32.4 | |||||||
2-stage | 2 | 1,800 | ||||||
3-stage | 3 | 680 | ||||||
Delta 2000 | 35.4 | 2,000 | 720 | |||||
1st stage | 910,000 | |||||||
2nd stage | 42,000 | |||||||
3rd stage | as above | |||||||
Delta 3000 | 35.4 | |||||||
original 3000 | 950 | |||||||
with PAM | 1,040 | |||||||
with PAM-D | 1,270 | |||||||
Delta 4000 | 39 | 1,360 | ||||||
Delta II 6000 | 39 | |||||||
6920 | 2 | 3,980 | ||||||
6925 | 3 | 1,450 | ||||||
Delta II 7000 | ||||||||
Delta III | 39 | 4 | 8,290 | 3,810 | 2,710 | |||
Delta IV | TK |